"为什么说物料衡算差1克,成本可能多花1万块?"
干了二十年发酵工艺的老王盯着车间报表直嘬牙花子。今儿咱就掰开揉碎说透这个让无数药厂头疼的"车间算账经",保准新手也能摸清门道!
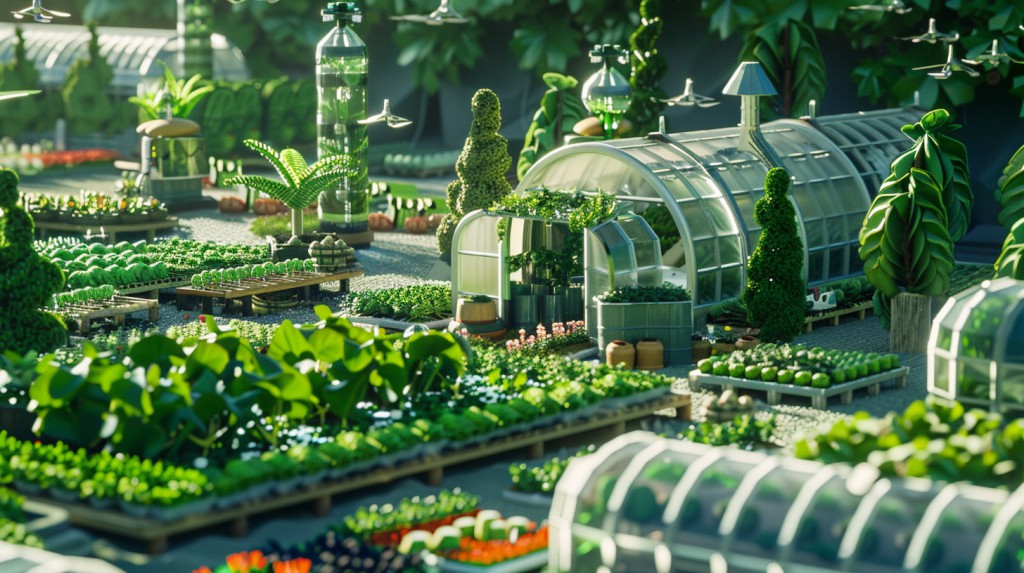
物料衡算到底是啥玩意儿?
简单说就是给车间装个"智能秤",把进料、转化、产出算得明明白白。以阿维菌素发酵为例,1吨玉米淀粉进去,理论上该出多少菌丝体、多少有效成分,实际产出差多少,这些数差就是成本黑洞。
看组触目惊心的数据:
- 国内90%发酵车间物料损耗率超8%(国际先进水平仅3%)
- 每差1%的淀粉转化率,年产500吨车间多烧120万燃料费
- 去年河北某药厂因衡算误差,整批报废损失380万
新手必踩的三大深坑
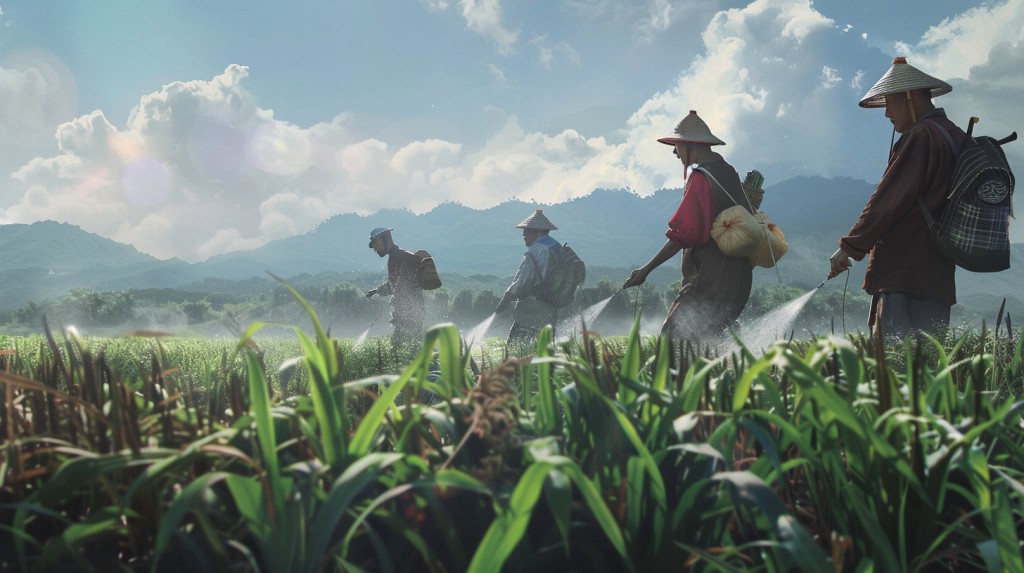
原料计量全靠手感
玉米淀粉含水量波动2%,直接导致菌种活性下降15%。山东李老板去年用目测法投料,三批发酵液pH值全超标。代谢产物算不清账
阿维菌素发酵会产生13种中间代谢物,漏算任意两种都会导致物料平衡表对不上。浙江某厂曾因未计入丙酸代谢,全年损耗虚高6.8%。设备残留视而不见
发酵罐每次清洗残留0.3%-0.5%物料,年产千吨的车间一年白扔15吨原料。更可怕的是这些残留物会污染下批菌种,武汉某车间就因此连续报废六批产品。
精准衡算四步通关法
第一步:建立基准模型
- 原料端:玉米淀粉、豆粕、葡萄糖等12项主料逐项建档
- 工艺端:精确记录灭菌温度(误差±0.5℃)、通气量(误差≤3%)
- 产出端:菌丝干重、阿维菌素效价、废水COD值三项必测
第二步:动态数据采集
监测点 | 采集频率 | 关键参数 |
---|---|---|
预处理罐 | 每15分钟 | 淀粉浓度、pH值 |
种子罐 | 每小时 | 溶氧量、菌浓 |
发酵主罐 | 每30分钟 | 效价、残糖量 |
下游处理 | 每批次 | 晶体收率、母液残留 |
第三步:异常值追凶
去年江苏某车间发现每批少算200kg物料,最后揪出是板框过滤机暗藏"吃料兽"——滤布夹层竟藏着3%的菌丝体!加装超声波清洗装置后,年省原料费87万。

第四步:数字化升级
沈阳某药厂上马MES系统后,衡算误差从7.2%降到0.8%。重点盯这三个模块:
- 电子批记录系统(自动生成物料流程图)
- 在线近红外分析仪(实时监控淀粉转化)
- 失重秤联动控制(投料精度达±0.1kg)
成本瘦身三板斧
蒸汽消耗砍一刀
采用三级热回收系统,灭菌工序蒸汽用量直降40%。按年产800吨规模算,年省燃动费超200万。废水变摇钱树
发酵母液含5%-8%有机质,浓缩干燥后可制成生物有机肥。广东陈总去年靠这招多赚160万副产品收入。菌渣再开发
阿维菌素菌丝体富含蛋白质,加工成水产饲料添加剂每吨卖8000元。浙江某厂去年消化1200吨菌渣,创收960万。
独家数据揭秘
行业内部监测显示,实施精细化物料衡算的药厂,三年内普遍实现:
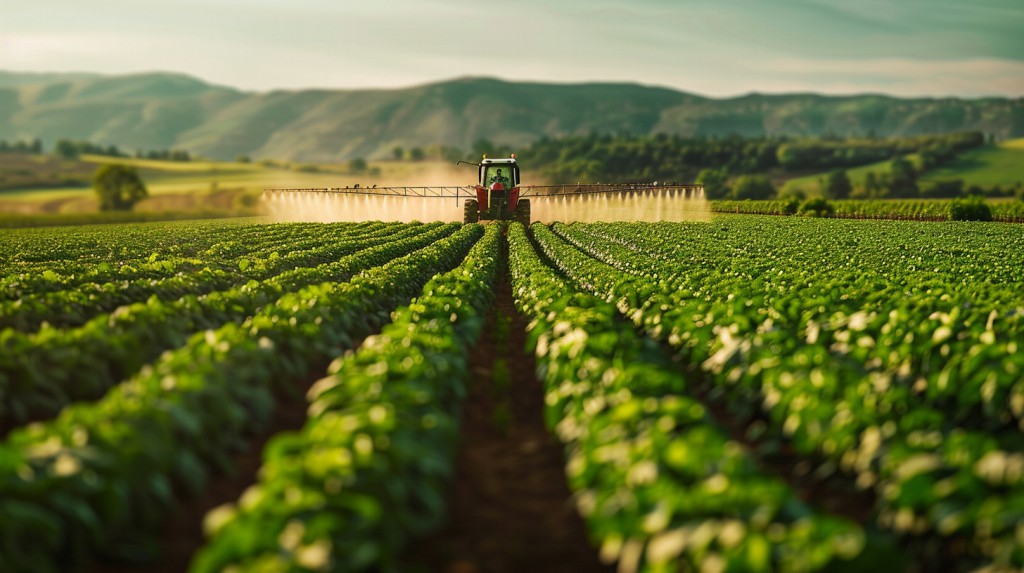
- 原料利用率提升22%-35%
- 单位能耗下降18-27元/公斤
- 批间差异缩小至±1.5%
更劲爆的是,掌握核心衡算技术的企业正在推行"按克计费"服务——帮中小药厂做一次车间级物料审计收费8-15万,但客户平均能收回10倍以上成本。
最后甩个硬核消息:新版GMP指南明确要求,2025年起所有发酵车间必须配备电子衡算系统。现在布局数字化改造的药厂,可申领最高300万的智能化升级补贴。这波政策红利不抓牢,到时候可别拍大腿!