生产农药中间体副产品,本质上是将主产线废料变废为宝的技术革命。以草铵膦中间体生产为例,每吨主产品可产生2-3吨含盐废水,其中氯化钠回收率可达85%。本文将揭秘从原料选择到三废处理的完整工艺链。
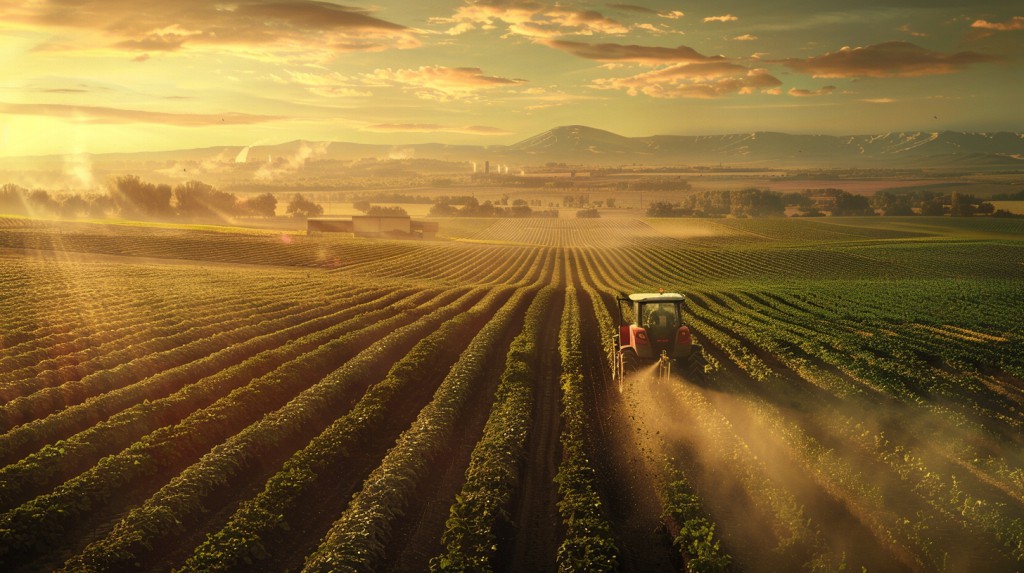
一、核心工艺路线选择:决定40%成本的关键
• 氯苄法:以2,6-二氯甲苯为原料,通过五氯化磷催化氯化,再水解腈化。该路线原料消耗降低30%,固体废料减少50%。个人见解:这条工艺路线特别适合生产除草剂中间体,但需注意光催化设备的防爆设计。
• 氨氧化法:采用邻硝基甲苯经中温氯化后催化氨氧化,主产物收率提升至70%。典型案例:山东某企业通过优化催化剂配方,将副产品氯化铵纯度提升到98.5%。
二、三废处理变财富:每吨废水多赚2000元
→ 废气:催化氧化装置可回收氰化氢制备氰化钠,某农药厂通过此技术年增收800万元
→ 废水:含盐20%的高盐废水经三效蒸发,可提取工业级氯化钠。关键参数:蒸发比控制在1:0.35,蒸汽消耗降低40%
→ 废渣:有机磷中间体废渣经高温焚烧,磷酸盐回收率可达75%
三、设备选型避坑指南:新手必看三大陷阱
1. 反应釜材质选择:处理含氯中间体必须用哈氏合金,某企业因错选316L不锈钢,三个月腐蚀穿孔损失200万
2. 离心机选型:含结晶盐物料需用吊袋离心机,普通三足式离心机易堵塞
3. 检测设备配置:必须配备离子色谱仪监测氯离子浓度,手持式电导率仪误差超30%
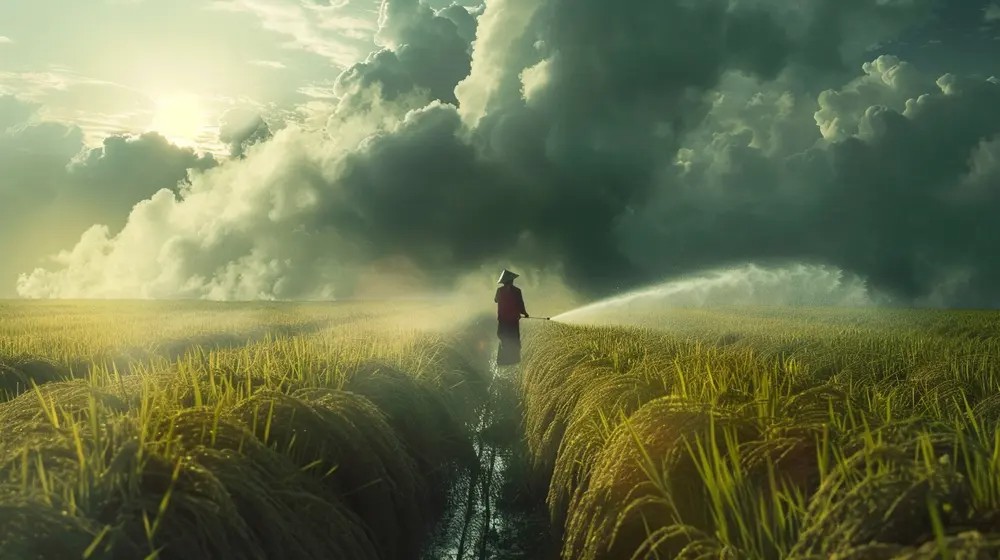
四、成本控制核心:这三个指标必须盯死
• 氰化钠替代技术:采用甲基亚膦酸二乙酯替代剧毒原料,安全成本直降60%
• 催化剂寿命:钯碳催化剂循环使用次数提升到15次,单次使用成本从3000元降至200元
• 蒸汽梯级利用:将120℃乏汽用于预热原料,某企业年省蒸汽费用150万元
独家预测:未来3年,微波催化技术和膜分离技术将颠覆传统工艺。浙江某研究院已实现微波辅助氯化反应时间缩短70%,能耗降低55%的实验数据。