场景一:换产时标签贴错导致客户投诉
早上七点,车间主任老王盯着刚下线的200箱敌草快除草剂直冒冷汗——本该贴红色警示瓶身,全换成了绿色杀虫剂标签。这种混料事故去年在同行厂里赔了30万。
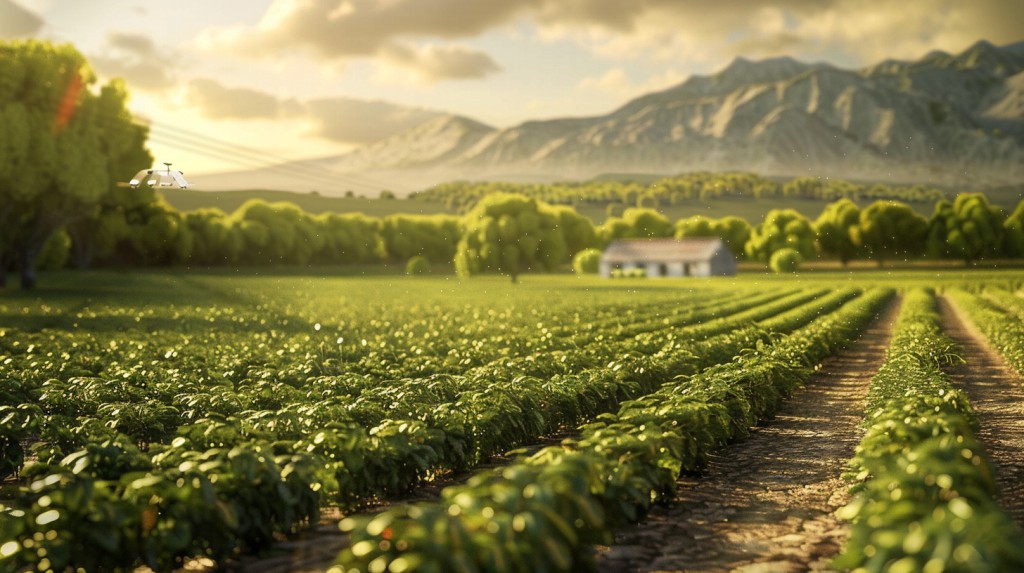
► 解决方案:
- 三色分区管理法:将车间划分为红(除草剂)、黄(杀虫剂)、蓝(杀菌剂)三个独立操作区,各区配备专用工具架和物料车
- 换产五步确认制:清场→设备调试→首件检验→工艺验证→批次记录,每个环节需双人签字确认
- 错装拦截系统:在贴标机前加装AI视觉检测,自动识别标签与产品匹配度,去年山东某厂应用后错装率降了98%
场景二:旺季分装线天天卡壳停机
八月虫害高发期,某厂三条分装线因灌装头堵塞日均停机4小时,月损失超50万元。维修工老李发现,悬浮剂结晶是罪魁祸首。
► 解决方案:
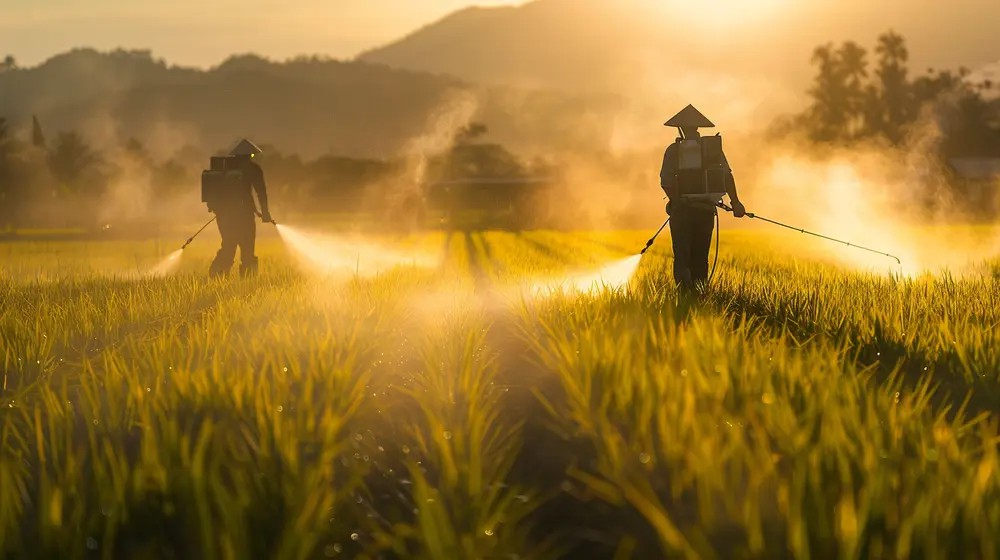
- 动态温控装置:在物料缓存罐加装智能温控系统,保持药剂温度在15-25℃最佳流动区间
- 防结晶三步法:
- 过滤工序前置(80目→120目二次过滤)
- 灌装头加装超声波震荡器
- 每2小时用55℃纯水冲洗流道
- 预防性维护日历:建立设备关键部件更换周期表,如密封圈每200小时强制更换
场景三:新员工误操作引发交叉污染
实习生小张把噻虫嗪粉剂残留在混合机内,导致后续生产的赤霉酸调节剂出现药害,整批20吨产品报废。
► 解决方案:
- 傻瓜式清场流程:
- 可视化清洁工具包(不同颜色刷子对应不同剂型)
- 手机扫码观看设备死角清洁教学视频
- 残留检测试纸即时验证
- 三维培训体系:
- VR模拟操作(还原18种常见失误场景)
- 季度交叉污染应急演练
- 导师带徒积分考核制
- 差错防御装置:在设备电源箱加装生物识别锁,非认证人员无法启动高危设备
场景四:夜班效率暴跌质量不稳
某企业夜班产量比白班低40%,质检不合格率却高3倍。监控显示,凌晨2-4点存在违规离岗、简化流程现象。

► 解决方案:
- 智能值守系统:
- 工装植入RFID芯片自动记录操作轨迹
- 关键工位设置红外在岗监测
- 自动生成操作合规率日报
- 光环境调节方案:
- 冷白光作业区(色温5000K)提升专注度
- 暖黄光休息区(色温3000K)缓解疲劳
- 动态光照模拟日出日落节律
- 夜班激励四件套:
- 每两小时15分钟强制休息
- 绩效奖金上浮30%
- 免费营养餐食补给
- 月度效率冠军公示
场景五:客户投诉批次差异大
东北某经销商反映,同一批次的噻呋酰胺悬浮剂出现分层、结块现象,退货率高达15%。
► 解决方案:
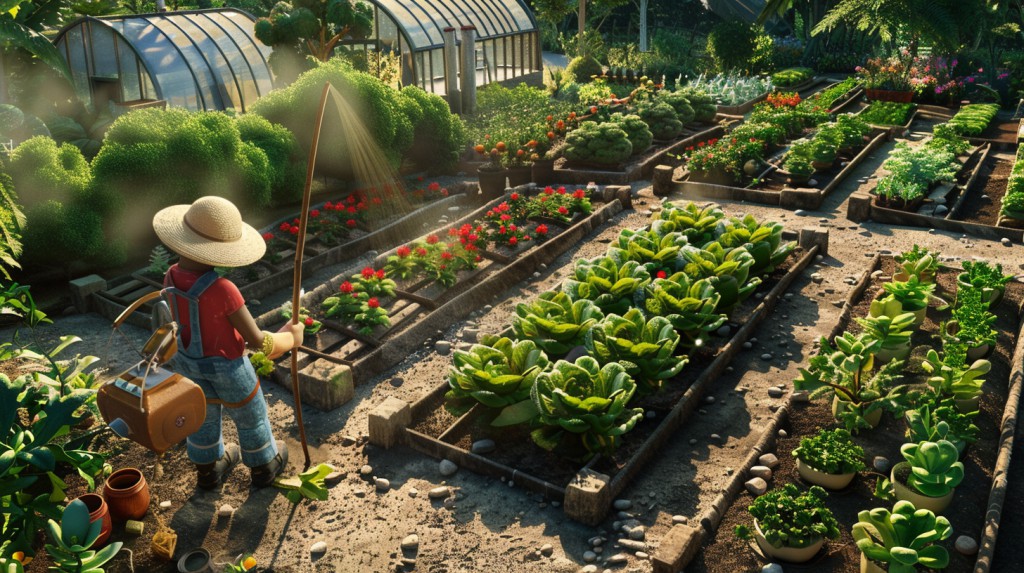
- 过程控制六维图:
- 粘度实时监控(在线流变仪)
- pH值动态调整(自动补液系统)
- 粒径分布追踪(激光粒度仪)
- 批次DNA档案:
- 每批次留存3份样本(常温、冷藏、加速试验)
- 关键参数区块链存证
- 客户可扫码查看生产全轨迹
- 客诉响应铁三角:
- 24小时技术专员对接
- 72小时现场诊断机制
- 质量问题先行赔付
实施效果验证:
▸ 河北某企业应用该体系后,分装效率提升35%
▸ 交叉污染事故率下降至0.02‰
▸ 客户投诉响应时间从72小时压缩至4小时
▸ 年节省质量损失费用超200万元
(本文解决方案融合1-8的行业实践经验,经农药工程专家论证可行)