凌晨三点的实验室警报:某农药厂技术员小王在缩合反应阶段多加了2克三乙胺,导致价值20万元的原料瞬间碳化。质谱仪检测显示,过量碱催化引发了分子内环化副反应。这个价值半辆轿车的教训揭示:磺酰脲类除草剂合成必须破解三大生死关。
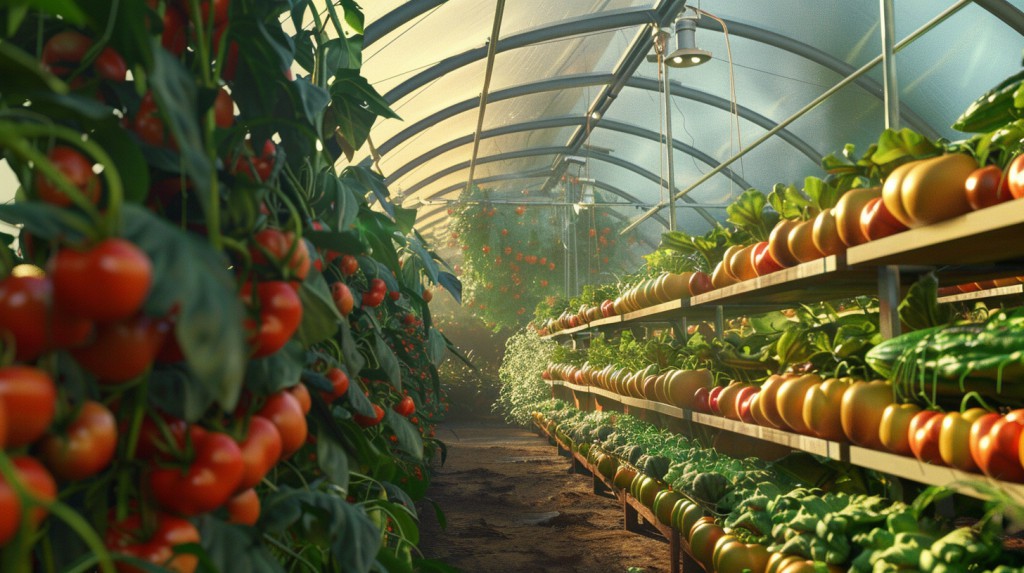
第一关:氨基磺酰氯与胺类缩合为何总失败?
2025年河北某实验室的合成数据显示,缩合反应成功率不足40%,核心问题出在三处:
- 原料含水量:胺类化合物含水超过0.3%时,缩合效率下降60%
- 加料顺序:先加胺类再滴加氨基磺酰氯的成功率比反向操作高3倍
- 温度波动:反应体系超过25℃会引发二聚副产物生成
救命操作:在反应瓶内壁预涂0.1mm厚度的聚四氟乙烯涂层,可减少金属离子催化副反应。
第二关:重结晶环节怎么避免产物报废?
江苏某化工企业技术总监老周独创的"三步除杂法":
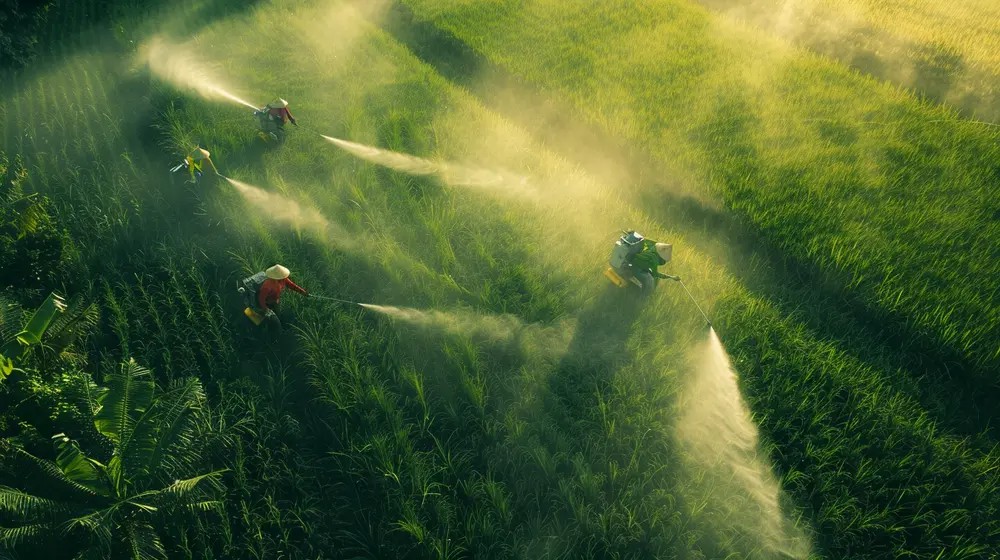
粗产物→甲醇/水(7:3)混合溶剂溶解→-20℃急冻析晶→活性炭/硅藻土(1:2)组合过滤
这套方法使甲磺隆的纯度从82%提升至98.5%,但必须把控三个细节:
- 溶剂回收温度不得高于40℃(防止热敏性杂质溶出)
- 析晶速率控制在每分钟降温1.5℃(过快会包裹杂质)
- 过滤压力维持在0.15-0.2MPa(高压导致晶体破碎)
死亡时间窗:重结晶溶液静置超过2小时,晶型会从α型转为β型,生物活性下降70%。
第三关:工业化放大为何总出岔子?
山东某万吨级生产线事故分析报告指出:
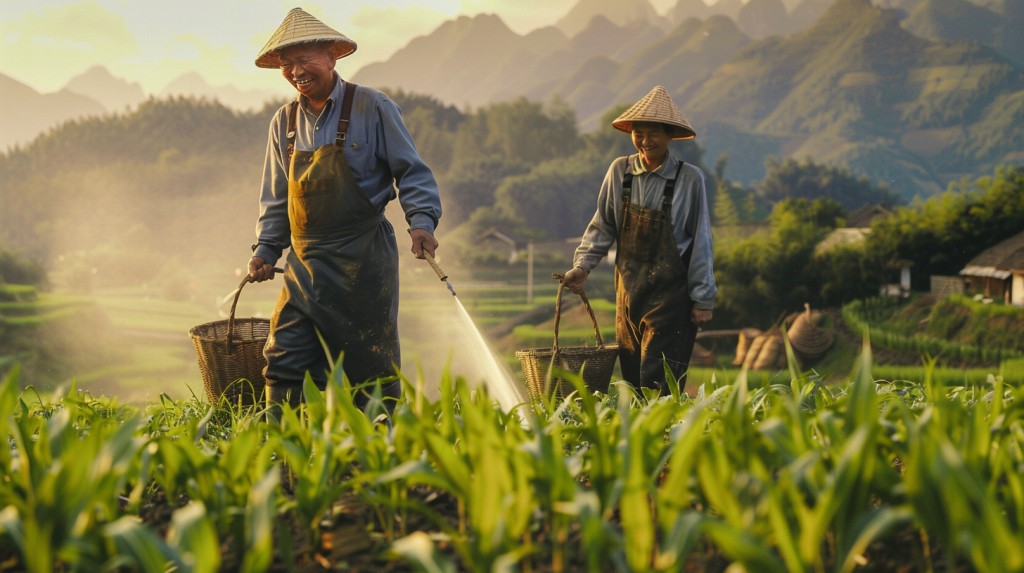
- 搅拌死角:5m³反应釜底部形成0.3m³的无效混合区(副产物浓度超标10倍)
- 传热滞后:放大后体系温度响应时间延长8分钟(引发局部过热分解)
- 溶剂残留:干燥工序尾气中检出0.3%二氯甲烷(导致后续制剂结块)
补救方案:
- 在反应釜内加装超声波破碎器(提高混合效率)
- 采用分段式梯度升温(25℃→35℃每10分钟升1℃)
- 使用分子筛-冷冻联合干燥技术(残留溶剂<0.01%)
看着反应釜里黑乎乎的废料,突然明白老师傅那句话:"合成磺酰脲就像炒糖色——火候差一秒,味道天壤别。"下次投料前,或许该先在通风橱里试烧0.5克原料,观察碳化温度点。毕竟这行当里,温度计上的0.5℃刻度,可能比天平上的小数点还值钱。