钠离子从何而来?
草甘膦合成过程中的氢氧化钠中和反应是主要来源,每生产1吨原药会产生约12-18kg钠盐残留。更隐蔽的污染源包括原料甘氨酸中含有的碳酸钠杂质,以及工艺水中的钠离子渗透。2025年湖北某企业的事故分析显示,其钠离子超标批次正是由于离子交换树脂柱失效导致。
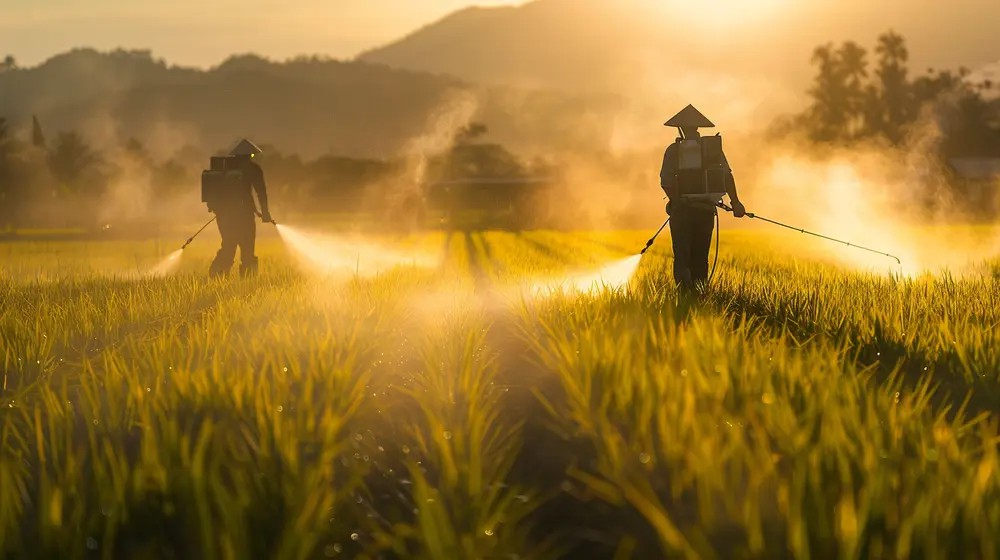
如何准确测定微量钠?
采用火焰原子吸收光谱法(FAAS)时,需特别注意标准曲线的非线性区间。当钠离子浓度在50-200mg/kg范围内,建议使用次灵敏线330.3nm替代主吸收线589.0nm。实际操作中,取1.0g样品经硝酸-过氧化氢微波消解后,定容至50ml比色管,加入2%氯化铯溶液消除电离干扰。
检测结果异常怎么排查?
某次平行样检测出现23.5mg/kg的偏差值,最终查明是移液管残留了清洗用的氢氧化钠溶液。系统性误差排查应遵循"三对照"原则:同批次试剂空白对照、已知浓度标准品对照、不同检测人员操作对照。当检出值超过GB/T 20684-2025规定的≤0.3%限值时,必须追溯最近三个生产批次的工艺参数。
样品前处理有哪些雷区?
粉碎工序中不锈钢设备可能引入微量钠污染,建议改用玛瑙研钵手动处理。消解温度控制尤为关键,超过180℃会导致草甘膦分子分解产生干扰物质。浙江质检院比对实验表明,采用梯度升温程序(120℃保持30分钟,再升至160℃维持20分钟)可使回收率提升至98.2±1.5%。

如何避免假阳性结果?
当检测到钠离子浓度突增时,首先排除实验室环境干扰。北方某企业曾因冬季供暖期钠含量异常升高,最终发现是暖气管道冷凝水混入样品。采用基质匹配标准品可有效消除基体效应,即用纯品草甘膦配制含钠标准溶液进行校准。
工艺环节怎样控制钠残留?
安徽某生产基地通过改造中和工序,将氢氧化钠溶液添加方式由批次投料改为在线计量泵连续注入,使钠离子波动范围从±15%缩小到±5%。在结晶工段增加三级逆流洗涤,每吨产品可减少钠盐携带量1.2-1.8kg。实时监测母液电导率,当数值超过800μS/cm时自动启动深度脱钠程序。
超标产品的挽救措施
对于钠含量在0.31%-0.35%的临界超标品,可采用重结晶精制工艺。将原药溶于60℃热水形成30%饱和溶液,加入晶种诱导定向结晶,可去除约65%的钠离子。山东某企业通过该方案,成功将价值80万元的待销毁产品转化为合格品。
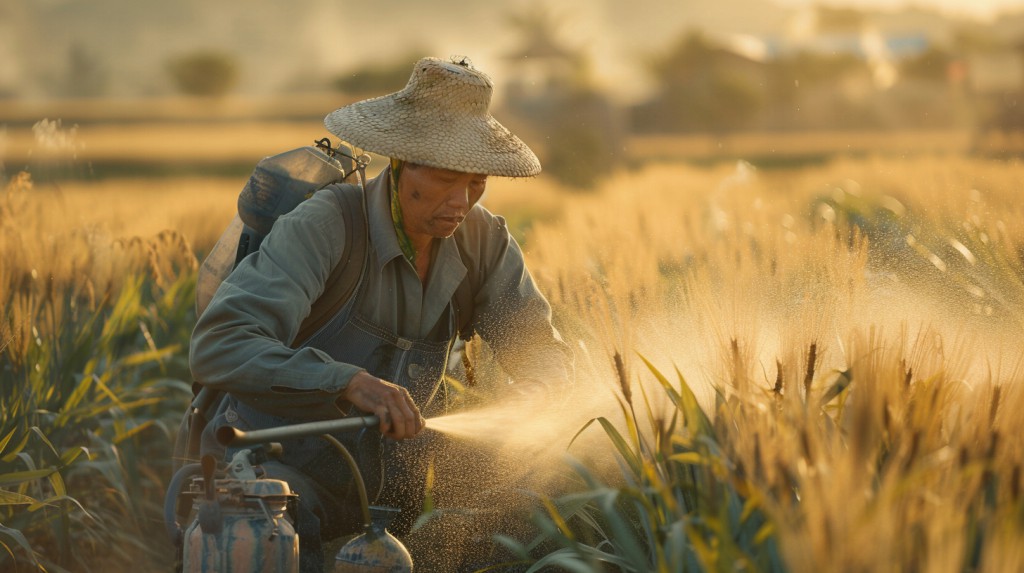
在广东肇庆的智能化生产线上,新安装的在线钠离子分析仪每15分钟自动采集数据。实施精准控制后,产品合格率从92%跃升至99.7%,每年减少原料浪费价值超200万元。当检测仪绿色指示灯第368次亮起时,这项看似微小的钠离子控制技术正在改写草甘膦行业的质量标准。